About How Consumer Electronics Distributors Manage Safety Stock
- What is safety stock, and why is it important for consumer electronics distributors?
- How do consumer electronics distributors balance safety stock with inventory costs?
- What factors are most critical when managing safety stock for consumer electronics?
- Can you explain the role of demand forecasting in optimizing safety stock levels?
- How do consumer electronics distributors mitigate the risks associated with overstocking?
1. Introduction to Safety Stock Safety stock is an essential component of inventory management, particularly for businesses in the consumer electronics industry. It refers to the extra stock maintained beyond the expected demand to prevent stockouts and ensure customer satisfaction. By maintaining safety stock, distributors can manage the unpredictability of consumer demand and maintain a competitive edge in the market. This article explores how consumer electronics distributors manage safety stock, the key factors involved, and the strategies they use to optimize their inventory levels.
2. The Role of Safety Stock in Consumer Electronics Distribution In the consumer electronics sector, safety stock plays a pivotal role in managing the high volume of products, frequent price changes, and short product lifespans. Distributors must carefully balance the need for stock availability with the risk of holding excess inventory, which can lead to increased storage costs and obsolescence. By maintaining appropriate levels of safety stock, distributors can ensure that customer demand is met without compromising on service levels or profitability.
3. Factors Influencing Safety Stock Management The management of safety stock is influenced by several factors, including lead time variability, fluctuating customer demand, the lifespan of electronic products, and inventory levels. Lead time variability refers to the unpredictable time required to replenish stock, which can be influenced by supplier lead times, transportation delays, and customs clearance times. Fluctuating customer demand adds complexity to inventory management, as it requires constant monitoring and adjustment of safety stock levels. The lifespan of electronic products is often short, making it essential for distributors to maintain low safety stock levels to avoid holding inventory for too long. Finally, inventory levels and storage costs are critical considerations, as excessive safety stock can lead to increased carrying costs.
4. Strategies for Managing Safety Stock Consumer electronics distributors employ various strategies to manage safety stock effectively. One common approach is the ABC analysis, which categorizes products based on their sales volume and importance to the business. Products classified as A are given the highest priority, while those classified as C are monitored less closely. Demand forecasting is another critical strategy, involving the use of historical data and market trends to predict future demand and optimize safety stock levels. Reorder point calculation is also a widely used method, which involves determining the optimal time and quantity to reorder stock to avoid stockouts while minimizing inventory holding costs. Safety stock formulas, such as the average demand plus safety stock formula, provide a quantitative basis for decision-making.
5. Optimizing Safety Stock Levels Optimizing safety stock levels requires a combination of accurate forecasting, risk assessment, and inventory management techniques. Distributors should analyze historical sales data to identify patterns and trends, enabling them to make informed predictions about future demand. Service level agreements (SLAs) can be used to set targets for order fulfillment and safety stock levels, ensuring high levels of customer satisfaction. Risk assessment and contingency planning are also essential, as they allow distributors to anticipate potential disruptions in the supply chain and adjust their safety stock levels accordingly. By integrating these strategies into their inventory management processes, consumer electronics distributors can optimize safety stock levels and achieve a balance between service quality and cost efficiency.
6. The Impact of Technology on Safety Stock Management Technology has revolutionized the way consumer electronics distributors manage safety stock. Automation tools, such as inventory management systems (IMS), enable real-time tracking of stock levels, reducing the risk of errors and improving decision-making. Machine learning and artificial intelligence (AI) are being increasingly used to analyze data and predict demand with greater accuracy, allowing distributors to optimize safety stock levels more effectively. Additionally, data analytics tools provide insights into inventory performance, helping distributors identify areas for improvement and reduce carrying costs. The use of technology not only enhances the accuracy of safety stock calculations but also improves the overall efficiency of inventory management processes.
7. Maintaining Accurate Safety Stock Records Maintaining accurate safety stock records is crucial for effective inventory management. Distributors should implement robust record-keeping practices, such as using digital tools to track inventory levels and updates. Regular audits and reviews of safety stock records are essential to ensure their accuracy and relevance. Integrating safety stock records into supply chain processes allows distributors to coordinate inventory management across the entire supply chain, reducing the risk of stockouts or overstocking. By maintaining detailed and up-to-date records, consumer electronics distributors can make informed decisions about safety stock levels and optimize their inventory strategies.
8. Challenges in Managing Safety Stock Despite the best efforts, managing safety stock in the consumer electronics industry presents several challenges. One major challenge is the complexity
OEM&ODM Factory wholesalers Wireless Charger, USB Charger and Adapter, Power Bank, USB C Docking Station, etc., -China Manufacturers & Wholesale Customized -Bethlar。
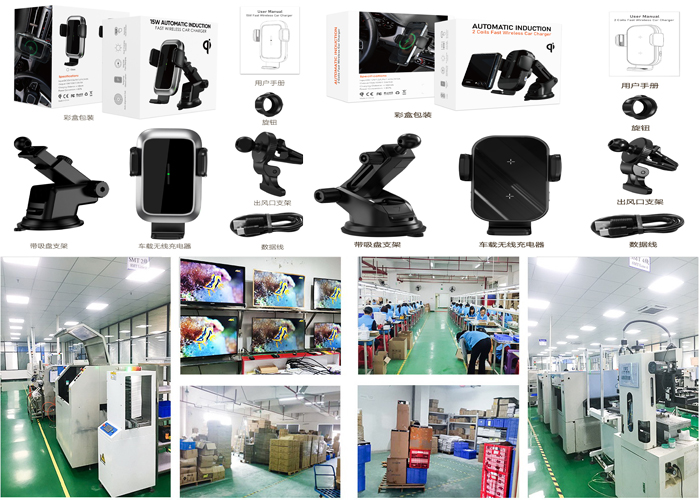
Dhongtai Co., Ltd., as a factory providing OEM services for foreign customers, plays a crucial role in the global supply chain. To ensure the stability of customers’ supply chains, reduce the risk of stockouts and enhance response speed, safety stock management has always been a key link.
1: We will retain an additional portion of inventory beyond the normal inventory to deal with the following uncertainties:
Demand fluctuations, supply delays, sudden increases in orders or shortened delivery times
For export-oriented OEM factories like Dhongtai Co., Ltd., a reasonable safety stock can enhance customer satisfaction, shorten the delivery cycle, and strengthen market competitiveness.
2: Establish a transparent communication mechanism with customers
Update the demand forecast of customers regularly (such as monthly/quarterly sales plans)
Clarify parameters such as the Lead Time (Lead Time) and the minimum order quantity (MOQ)
Use shared systems or platforms (such as ERP integration, Google Sheets, Airtable)
3: Set a reasonable safety stock level based on customer demands
For products with high sales volume and low variability, a lower safety stock can be set.
For new products or seasonal products, the proportion of safety stock should be appropriately increased.
4: Optimize production and supply chain collaboration
Internal measures of the factory
Enhance production flexibility (such as modular design and rapid line changeover capability)
Shorten the Lead Time Reduction
Establish a safety stock of key raw materials (especially imported materials)
External collaboration
Cooperate with logistics companies to establish stable transportation channels (such as regular liner services and air charter flights)
5: The customer is a well-known wholesale brand of consumer electronics in North America
The annual order volume is approximately 200,000 units, with a large number of SKUs and significant fluctuations in demand
The main challenges: Long sea transportation cycle (30-45 days), and a sharp increase in demand during peak seasons
Solution:
Share ERP data with customers and update sales forecasts monthly
Set up a dynamic safety stock model and automatically calculate the inventory threshold
Reserve 10%-15% of the safety stock in the third-party warehouse in the central United States designated by the customer
Establish an “emergency additional order channel” and activate the air cargo replenishment mechanism in response to sudden demands
Outcome:
The out-of-stock rate has decreased by 60%
The average delivery cycle has been shortened to within 7 days
Customer satisfaction has improved and the renewal rate has increased